How to master your QA processes plus
the #1 thing to avoid!
Matt Hopson,
Quality & Sustainability Manager
Founder at QA Audit NZ
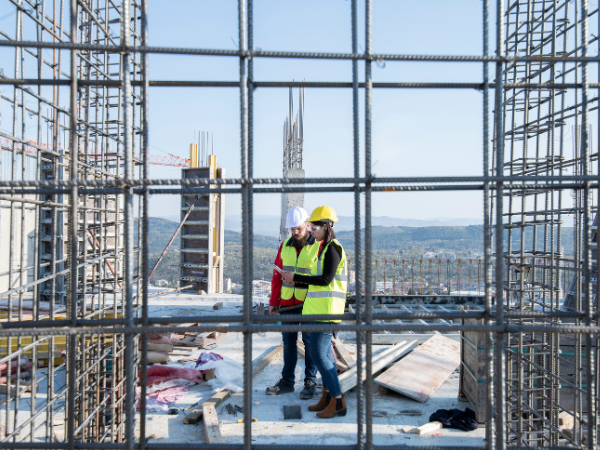
What is Quality Assurance in Construction and why does it matter?
Quality Assurance (QA) in construction, distinct from Quality Control (QC), revolves around proactive strategies to ensure all stakeholders understand and agree upon project requirements. QA involves implementing measures that guarantee compliance, transparency, traceability, and accountability throughout the construction process. This proactive approach is critical in delivering high-quality projects that are not only safe, compliant, and sustainable but also profitable. Ultimately, QA is about embedding excellence in every facet of the construction process, far beyond mere adherence to standards.
Quality Assurance (QA) in construction is meticulously designed to ensure that processes, methodologies, inspections, and tests are comprehensively understood and agreed upon before any construction begins, and effectively monitored and documented upon completion.
The core outcomes of QA include:
Consistency and uniformity | Enhanced safety | Regulatory and legal compliance | Cost efficiency | Client satisfaction | Sustainability | Operations and innovation |
Ensuring all aspects of construction meet uniform standards across projects, which is crucial for structural integrity and aesthetic coherence. | Prioritising the safety of construction sites and finished structures, thereby protecting workers, future users, and the public. | Aligning construction practices with applicable laws and regulations to avoid legal repercussions and ensure ethical standards. | Minimising financial waste through efficient resource management, reducing the need for costly rework, and preventing project delays. | Delivering projects that fulfill or exceed client expectations, thereby bolstering the firm’s reputation and enhancing customer loyalty. | Promoting environmentally responsible construction practices and the use of sustainable materials to reduce environmental impact. | Driving continuous improvement and encouraging the adoption of innovative construction techniques and technologies. |
These outcomes are not only fundamental to the long-term success and sustainability of individual projects but are also essential for advancing the overall industry. They benefit a wide array of stakeholders, including project teams, clients, and the community at large, ensuring that the impacts of construction are positive and far-reaching.
Addressing the question of roles and responsibilities in quality management within construction can seem complex, but clarity emerges with the right training.
Quality Management System (QMS): A QMS, or in many contemporary contexts, an Integrated Management System (IMS), encompasses ISO 9001 for Quality Management, along with Environmental and Safety standards under ISO 14000 and ISO 45001. This system ensures that a company has robust policies and procedures to successfully manage and complete projects, enhancing client confidence.
What is the difference between ITPs & ITRs?
Inspection and Test Plans (ITPs): These documents are pivotal for all project stakeholders. They outline critical checkpoints or interventions such as 'Hold Points'—where an inspection must occur before work can proceed—and 'Document Reviews' for approvals on necessary documentation. ITPs guide stakeholders on compliance with specifications and detail which tests or records are required at each intervention point. It's crucial that a comprehensive method statement and anticipated Inspection and Test Records (ITRs) accompany each ITP. Remove the need for cumbersome paperwork by streamlining and digitising the way ITPs are managed.
Inspection and Test Records (itrs): These are the documented outcomes required at each intervention point, agreed upon when stakeholders approve an ITP. ITRs are essential for compiling the Quality Assurance handover package at the project's conclusion.
All these elements are interrelated: the QMS provides a broad framework within which ITPs are formulated and ITRs are executed. Their effective implementation is essential for meeting the project’s quality standards. Through collaboration and clear communication across various departments, these systems help ensure that all team members understand their roles and contributions towards the overarching quality objectives, thus maintaining high standards throughout the construction process.
#1 reason companies fail at QA?
The primary reason QA fails in construction frequently stems from a lack of clarity and understanding regarding project requirements. This challenge underscores the critical role of Inspection Test Plans (ITPs) and Quality Assurance (QA) processes in aligning all stakeholders. Poor communication and inadequate engagement among the parties involved—contractors, subcontractors, design teams, and clients—further exacerbate the issue. When interactions are not clear, consistent, and regular, misunderstandings are likely to arise, leading to errors and non-compliance with established quality standards. Addressing these communication gaps is essential for ensuring that everyone is aligned and quality objectives are met effectively. When organisations take on digitise the way manage their QA it addresses the primary reason QA fails - miscommunication and misunderstanding of project requirements. By ensuring that all stakeholders have a clear and consistent understanding of the QA processes this mitigates the risks associated with poor communication, thereby enhancing the overall success of our quality assurance efforts.
Top tips on avoiding risk when it comes to QA management:
👉 Have your QA requirements agreed upfront
👉 Review and approved by all stakeholders
👉 Implement as per plan
👉 But most importantly - have full transability or records and progress for hand back
To effectively manage QA risk, it's crucial to have all QA requirements agreed upon, reviewed, and approved by all stakeholders upfront. Once these prerequisites are established, the focus should shift to implementing the plan precisely as outlined. Equally important is maintaining comprehensive traceability of records and progress throughout the project, which is essential for a smooth handover process. This structured approach not only mitigates risk but also ensures transparency and accountability at every stage of the project.
Common misconceptions
#1 misconception in the New Zealand Construction sector is that you don't need approval for QA before commencing work (it's actually essential!). Many contractors begin projects without approved Inspection Test Plans (ITPs), setting the stage for potential issues down the line. Additionally, there is often a misunderstanding of the commercial implications associated with Hold Points and the significance of Witness Points, both crucial elements of the construction monitoring regime.(cm1-cm5) this determines H or W.
Moreover, having a detailed checklist is arguably more important than the ITP itself, as it guides the QA process more effectively. Equally challenging is the management of QA documentation; ensuring it is readily accessible later is a hurdle that needs addressing. It's also important to clarify that building consents and ITPs are the same thing; ITPs cover more requirements and contractors must start including BC conditions into their ITPs. Furthermore, the functions of Non-Conformance Reports (NCRs) and Requests for Information (RFIs) are often misunderstood.
About | Quality Assurance Audit NZ
Matt developed the QA in Construction training program to address these issues and help organisations simplify their QA. This comprehensive training ensures that all stakeholders come away with a clear understanding and practical view of how the QA process should work, can work and how to have it implemented successfully.
Click here to get a free consultation.
CONQA 30-Day FREE Trial
Construction field management software for contractors
Checklists | Sign-offs | Reporting | Variations | Progress tracking